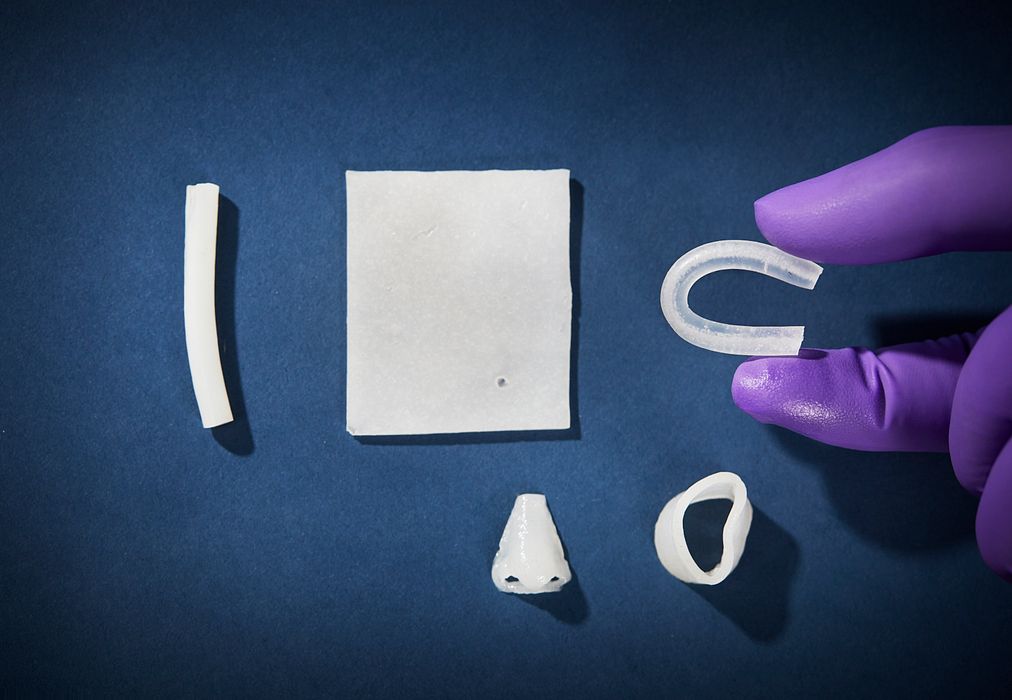
In the development of medical technology products, there is a great demand for new naturalistic materials suitable for integration with the body. Introducing materials into the body comes with many risks, such as serious infections, among other things. Many of the substances used today, such as Botox, are very toxic. There is a need for new, more adaptable materials.
In the new study, the Chalmers researchers developed a material consisting solely of components that have already been shown to work well in the body.
The foundation of the material is the same as plexiglass, a material which is common in medical technology applications. Through redesigning its makeup, and through a process called nanostructuring, they gave the newly patented material a unique combination of properties. The researchers' initial intention was to produce a hard bone-like material, but they were met with surprising results.
“We were really surprised that the material turned to be very soft, flexible and extremely elastic. It would not work as a bone replacement material, we concluded. But the new and unexpected properties made our discovery just as exciting,” says Anand Kumar Rajasekharan, PhD in Materials Science and one of the researchers behind the study.
The results showed that the new rubber-like material may be appropriate for many applications which require an uncommon combination of properties – high elasticity, easy processability, and suitability for medical uses.
“The first application we are looking at now is urinary catheters. The material can be constructed in such a way that prevents bacteria from growing on the surface, meaning it is very well suited for medical uses,” says Martin Andersson, research leader for the study and Professor of Chemistry at Chalmers.
The structure of the new nano-rubber material allows its surface to be treated so that it becomes antibacterial, in a natural, non-toxic way. This is achieved by sticking antimicrobial peptides – small proteins which are part of our innate immune system – onto its surface. This can help reduce the need for antibiotics, an important contribution to the fight against growing antibiotic resistance.
Because the new material can be injected and inserted via keyhole surgery, it can also help reduce the need for drastic surgery and operations to rebuild parts of the body. The material can be injected via a standard cannula as a viscous fluid, so that it forms its own elastic structures within the body. Or, the material can also be 3D printed into specific structures as required.
“There are many diseases where the cartilage breaks down and friction results between bones, causing great pain for the affected person. This material could potentially act as a replacement in those cases,” Martin Andersson continues.
A further advantage of the material is that it contains three-dimensionally ordered nanopores. This means it can be loaded with medicine, for various therapeutic purposes such as improving healing and reducing inflammation. This allows for localised treatment, avoiding, for example, having to treat the entire body with drugs, something that could help reduce problems associated with side effects. Since it is non-toxic, it also works well as a filler – the researchers see plastic surgery therefore as another very interesting potential area of application for the new material.
“I am now working full time with our newly founded company, Amferia, to get the research out to industry. I have been pleased to see a lot of real interest in our material. It’s promising in terms of achieving our goal, which is to provide real societal benefit,” Anand concludes.
Read the study, “ Tough Ordered Mesoporous Elastomeric Biomaterials Formed at Ambient Conditions” in the scientific journal ACS Nano.
The path of the research to societal benefit and commercialisation, through start-up company Amferia and Chalmers Ventures
In order for the discovery of the new material to be useful and commercialised, the researchers patented their innovation before the study was published. The patent is owned by start-up company Amferia, which was founded by Martin Andersson and Anand Kumar Rajasekharan, two of the researchers behind the study, as well as researcher Saba Atefyekta who recently completed a PhD in Materials Science at Chalmers. Anand is now CEO of Amferia and will drive the application of the new material and development of the company.
Amferia has previously been noted for an antibacterial wound patch developed by the same team. Amferia now has the innovation of both the new nano-rubber and the antibacterial wound patch. The development of the company and the innovations' path to making profit are now being carried out in collaboration with Chalmers Ventures, a subsidiary of Chalmers University of Technology.
More about the research: interdisciplinary collaboration at Chalmers
Several of Chalmers’ departments and disciplines were involved in the study. In addition to researchers at the Department of Chemistry and Chemical Engineering, Marianne Liebi, Assistant Professor at the Department of Physics, was a co-author of the article. She has developed a technology to make it possible to investigate the order of materials by means of x-ray irradiation, to see how the nanostructures relate to each other in the material. In the ongoing work, an industrially feasible process for production of the material will be developed. This will be done in collaboration with the Department of Industry and Materials Science.
For more information, contact:
Martin Andersson, Professor in Chemistry
+46317722966
martin.andersson@chalmers.se
Anand Kumar Rajasekharan, PhD in Materials Science and CEO of Amferia
+46 (0)762 981238
anandk@amferia.com